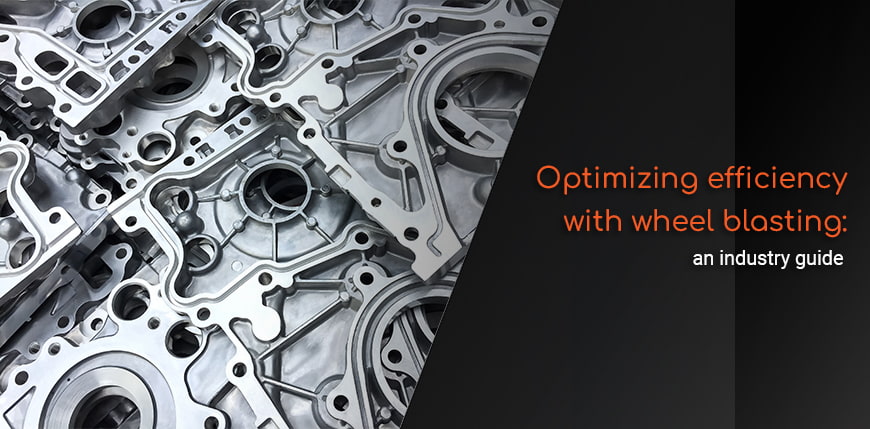
Wheel blasting is renowned for its efficiency and effectiveness in processing large batches of components within production lines. This comprehensive guide delves into the intricacies of the wheel blasting process, highlighting its operational mechanics, the variety of abrasives employed, and the importance of expert guidance to maximize its potential.
Understanding the wheel blasting process
Wheel blasting, an airless operation, employs a turbine to propel abrasive media at high velocity toward the workpiece. This process is instrumental in removing contaminants like mill scale and old coatings, strengthening materials, and creating an anchor profile for subsequent treatments. The use of abrasives like steel shot and grit, cut wire, and stainless steel shot in wheel blast machines illustrates the process's versatility.
The mechanics of wheel blasting
- Abrasives supply: The process begins with feeding abrasive material, typically small metal balls, into a rotating wheel's core.
- Acceleration: Centrifugal force ejects the abrasives through wheel openings onto a drum that directs them onto another wheel with blades.
- Impact: The second wheel hurls the abrasives against the workpiece with considerable speed, achieving effective surface treatment.
- Recycling: The operation occurs within an enclosed chamber, allowing for the continuous reuse of abrasives, separating them from the waste material.
Advantages of wheel blasting
- Speed: Wheel blasting provides rapid cleaning and surface preparation, significantly enhancing productivity, especially for large components.
- Efficiency: This method eliminates the need for compressed air, reducing operational costs and energy consumption.
- Consistency: A balanced working mix, crucial for optimal results, ensures a uniform quality of finish across batch-processed items.
Considerations and expert guidance
Despite its numerous benefits, wheel blasting presents challenges, such as the potential for damaging sensitive products due to the high-speed impact and its limitations with non-uniform or flat components. Choosing the right abrasive and maintaining a balanced working mix are critical for success, necessitating expert input.
Professionals in the field can provide insights into selecting suitable abrasives, adjusting machine settings, and troubleshooting common issues. Their expertise ensures the wheel blasting process is tailored to specific industry requirements, maximizing both the quality and efficiency of surface treatment operations.
Conclusion
Wheel blasting is a powerful technique within the industrial finishing arsenal, offering a high degree of efficiency and effectiveness for batch processing. By understanding the process's dynamics and leveraging the right abrasives under expert guidance, industries can harness wheel blasting's full potential, achieving superior surface preparation and finishing outcomes. As with any advanced technology, the collaboration with seasoned professionals is key to unlocking wheel blasting's benefits while mitigating its limitations.