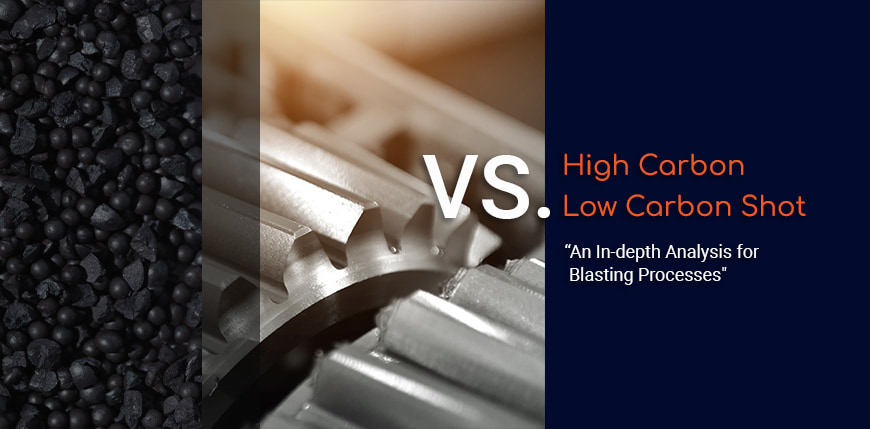
Integrating expert guidance into the selection process of high carbon and low carbon shots is paramount for achieving optimal blasting outcomes. As each type of shot offers distinct advantages tailored to specific industrial needs, the nuanced choice between them hinges on a thorough understanding of their applications, durability, and how they align with the objectives of the blasting process.
High Carbon Shot: Flexibility in Application
High carbon shot's key advantage lies in its adjustable hardness, which broadens its utility across a variety of surface preparation tasks. This characteristic allows operators to tailor the blasting process to achieve precise finishes, especially on surfaces requiring aggressive treatment. The option to choose between shot and grit forms further enhances its adaptability, making high carbon shot a versatile choice for industries tackling challenging coatings and surface preparations.
Low Carbon Shot: Economical and Gentle
Conversely, low carbon shot, with its singular hardness level and form, offers a softer approach that minimizes the risk of substrate damage. Its less brittle nature translates to lower consumption rates and, potentially, reduced operational costs. This makes low carbon shot especially suitable for delicate applications, such as in the aluminum parts and foundry sectors, where preserving the integrity of the workpiece is as crucial as the cleaning or decalcification itself.
Deciding Between High and Low Carbon Shots
The decision to use high or low carbon shot is particularly critical in applications focused on decalcification and cleaning, with industries like coil processing, foundries, and aluminum manufacturing facing these choices more frequently. The selection process must consider the specific requirements of the task at hand, balancing the need for efficiency, cost-effectiveness, and the preservation of the material's integrity.
In navigating these decisions, the role of professional guidance cannot be overstated. Specialists in abrasive blasting can provide tailored advice to optimize the blasting process, leveraging their expertise to select the most appropriate type of shot, adjust blasting parameters, and implement best practices. This expert input ensures that each blasting operation is not only effective but also maximizes resource efficiency and achieves the desired outcomes in surface treatment.
Through careful consideration of the unique properties and benefits of high carbon and low carbon shots, informed by professional insights, industries can enhance their blasting operations to meet the highest standards of quality and efficiency. This approach underscores the importance of strategic selection and optimization in abrasive blasting, driving advancements in surface treatment technologies.