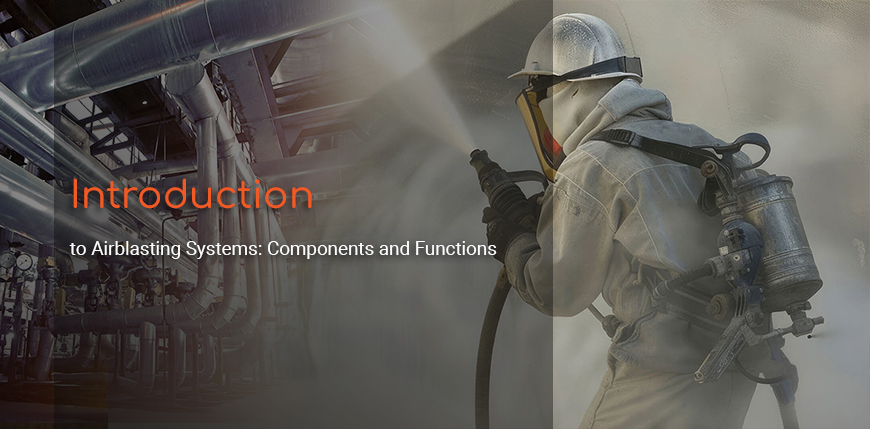
Whether it's removing rust, scale, or old paint, airblasting offers a versatile and efficient solution. However, to achieve optimal results, it's important to understand the components and functions of an airblasting system and how they work together.
Key Components of an Airblasting System
Airblasting systems consist of several critical components that work in unison to ensure effective performance. Each component plays a specific role in the blasting process:
1. Compressor:
The compressor is the heart of any airblasting system, providing the compressed air that powers the entire operation. It delivers a consistent air supply that propels the abrasive material toward the surface being treated. Choosing the right compressor capacity is crucial, as it directly affects the performance of the entire system. If the compressor is too small, the system will lack the necessary pressure, reducing effectiveness. It must be sized to deliver the right volume of air at the right pressure for all the blasters.
3. Blast Hose:
The blast hose connects the blast pot to the nozzle. It must be durable enough to handle the flow of abrasive material without wearing out prematurely. It’s essential to choose the correct diameter of the hose based on the size of the nozzle and the power of the compressor. Incorrect hose diameter can lead to a loss of pressure and reduced efficiency.
4. Nozzle:
The nozzle is where the compressed air and abrasive media converge before being propelled toward the target surface. Nozzle selection is key to achieving the desired result. Straight nozzles are used for precision work, while Venturi nozzles are ideal for covering larger surfaces. Over time, nozzles wear out and should be replaced when their diameter increases by more than 10% of the original size.
5. Deadman Switch:
Safety is paramount in airblasting operations. The deadman switch is a handheld device that allows the operator to immediately stop the flow of abrasive by releasing the trigger. This prevents accidental damage or injury and gives the operator complete control of the process.
6. Airwash Separator:
In systems where abrasive recycling is possible, the airwash separator ensures that the abrasive is cleaned and separated from dust and debris before being reused. This increases the system’s efficiency and reduces waste.
7. Dust Collector:
The dust collector is responsible for capturing and filtering the dust generated during the blasting process. It ensures that the work environment remains clean and safe, preventing airborne contaminants from affecting worker health and equipment performance.
Why Choosing the Right Equipment Matters for Performance and Safety
Selecting the appropriate equipment for airblasting is essential to ensure both optimal performance and safety. When the system components are correctly matched, they work harmoniously to deliver powerful and efficient results. For example, using a nozzle that is too large for the compressor will result in lower pressure, reducing the effectiveness of the blasting process.
Moreover, ensuring that the hoses, nozzles, and other components are in good condition prevents potential accidents. Over time, wear and tear can compromise the integrity of these parts, leading to leaks, inefficiencies, and even dangerous blowouts.
Importance of Regular Maintenance and Inspection
Regular maintenance is crucial to the longevity and performance of any airblasting system. Components such as hoses, nozzles, and the blast pot undergo significant wear due to the high-pressure nature of the operation. Conducting frequent inspections allows you to identify worn-out parts before they cause larger issues.
· Hose and Nozzle Inspection: Look for signs of wear such as cracks, thinning, or loss of pressure. Replace any parts that show visible damage.
· Blast Pot Maintenance: Ensure that the blast pot is free from any obstructions that could impede the flow of abrasive material. Periodically clean the pot to remove built-up material that could affect performance. The blasting pot must absolutely be airproof.
· Dust Collector Checks: Make sure that the dust collector is functioning properly to maintain a clean and safe working environment. Regularly empty the collector and replace any filters as needed.
By investing time in routine maintenance, you prevent unexpected breakdowns and ensure that your airblasting system operates at peak performance.
Partnering with experts who can provide guidance on equipment selection and maintenance schedules can save significant time and cost in the long run. With proper care and attention, your airblasting system will deliver consistent, high-quality results for years to come.