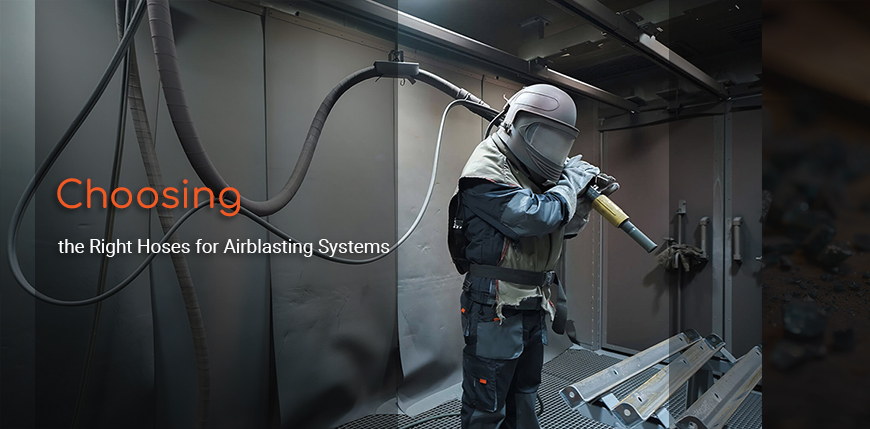
The right hose can significantly impact performance, while the wrong choice may lead to reduced productivity, safety risks, or even equipment failure. This article explores the importance of selecting the right hose for airblasting and provides insights into key considerations such as hose material, diameter, and maintenance.
Understanding the Role of Hoses in Airblasting
Airblasting systems rely on high-pressure air to propel abrasive media at a target surface, cleaning or preparing it for further processing. The hose carries this air and abrasive mix from the air compressor or blasting pot to the nozzle. Its ability to withstand both the pressure and the abrasive materials is essential for efficient and safe operation.
A well-chosen hose ensures minimal air pressure loss and a smooth flow of abrasive material, leading to consistent blasting results. On the other hand, an incorrectly matched or poorly maintained hose can result in pressure drops, reduced abrasive flow, and even potential accidents.
Key Considerations When Selecting a Hose
1. Hose Material and Durability:
The materials used in the construction of a hose must be abrasion-resistant to withstand the constant flow of abrasive particles. Reinforced rubber or polyurethane hoses are commonly used due to their durability and flexibility. The choice of material also depends on the specific abrasive media being used.
Tip: For tougher abrasives like slag or corundum, it is advisable to choose hoses made from highly abrasion-resistant materials such as those reinforced with steel wire.
2. Diameter and Length of the Hose:
The diameter of the hose directly affects the air pressure and abrasive flow. A hose that is too narrow will restrict the flow, reducing the impact force of the abrasive, while a hose that is too wide may lead to pressure drops and inefficiency. The length of the hose also plays a role; longer hoses will cause more pressure loss over distance, so it's essential to choose the correct length for your specific application.
Tip: Follow the manufacturer’s recommendations to select the appropriate diameter and length, ensuring compatibility with the air compressor and nozzle.
3. Pressure Rating:
Hoses used in airblasting must be able to withstand the high pressures typically required for blasting, usually between 7 and 10 bars (100 to 145 psi). It’s important to choose a hose with a pressure rating that exceeds the operating pressure of your system to account for potential spikes and ensure safety.
Tip: Regularly inspect the hose for signs of wear or damage, particularly around the couplings, to prevent sudden hose failure.
Maintaining Hoses for Optimal Airblasting Performance
1. Inspect for Wear and Tear:
Hoses are subjected to significant wear due to both the high pressure and the abrasive particles they carry. Over time, the interior lining of the hose can become worn, reducing the efficiency of the blasting process and increasing the risk of failure.
Tip: Inspect the hoses regularly for visible signs of wear, such as cracks or bulges. Pay special attention to the natural bends in the hose, as these areas tend to experience the most wear. To evaluate the wear of a hose, there is a simple method: find out the bending radius of the hose on the data sheet, then bend it to reach the radius, if it makes an angle or a fold somewhere you should replace it. Another simple method: tight the hose with your hand in sensible areas, if you feel a soft point, replace the hose. The hose must remain tough on all its length.
2. Check Hose Couplings and Connections:
The integrity of the hose couplings and connections is critical for maintaining air pressure and ensuring safety. Loose or damaged couplings can cause pressure drops or, in extreme cases, the hose can disconnect during operation, posing a serious safety risk.
Tip: Always ensure that couplings are tightly secured and free from damage. Regularly check for air leaks at the connections, which can be a sign of worn or faulty couplings.
3. Replacing Worn Hoses:
Hoses should be replaced when visible signs of wear appear or when the internal diameter becomes enlarged due to abrasive wear. A worn hose can reduce the blasting efficiency and pose a safety risk.
Tip: Replace the hose when its internal diameter has increased by 10% compared to its original size, as this indicates significant wear that could compromise performance.
Monitoring Hose Performance
Proper monitoring of hoses in an airblasting system can help avoid unexpected breakdowns and maintain system performance. Using tools like pressure gauges and flow meters, operators can keep track of pressure drops and airflow through the hose. A sudden change in these metrics could indicate that the hose is worn or has developed a blockage.
Tip: A sieve kit can be used to analyze the abrasive media passing through the hose to ensure consistent particle size and flow.
Safety Considerations for Hose Maintenance
Maintaining the hose is not just about performance but also about ensuring operator safety. Hoses that are worn or improperly connected can fail during operation, causing the abrasive media to escape and potentially harm the operator.
Tip: Always wear appropriate PPE (personal protective equipment) such as safety boots, gloves, helmets, and face shields when working with airblasting systems, especially when replacing or inspecting hoses. It is also recommended to use reflective strips on PPE for better visibility in low-light environments, which are common in airblasting operations.
Choosing and Maintaining the Right Hose for Optimal Results
In airblasting systems, hoses are critical components that directly impact the performance, safety, and efficiency of the operation. Selecting the right hose, based on material, diameter, and pressure rating, ensures that the system runs smoothly and effectively. Regular monitoring and maintenance, including inspecting for wear and tear, checking couplings, and replacing worn hoses, are essential for keeping the system in top condition.
A proactive approach to hose maintenance not only improves airblasting efficiency but also enhances safety and reduces long-term costs associated with downtime and repairs. By choosing high-quality hoses and following best practices for maintenance, operators can ensure consistent, reliable, and safe airblasting performance.