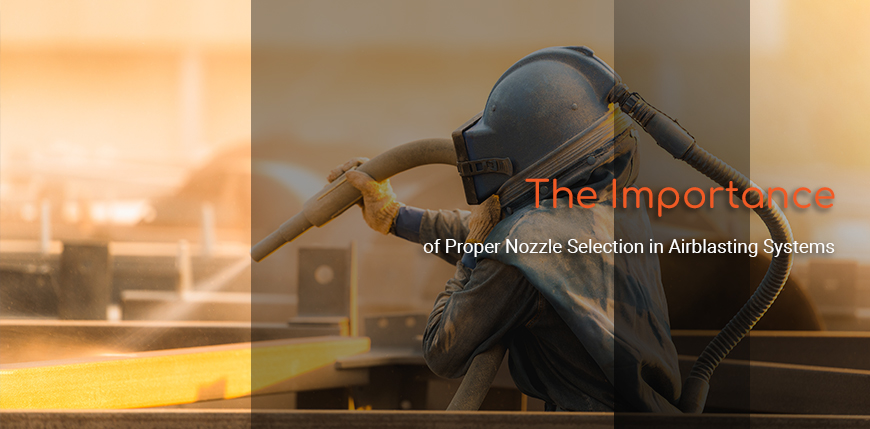
Whether you’re removing rust, descaling metal, or preparing surfaces for coating, the right nozzle can significantly impact the efficiency and effectiveness of the airblasting process. This article explores the different types of nozzles used in airblasting, their benefits, and why selecting the correct nozzle is crucial for performance and safety.
The Function of Nozzles in Airblasting
Nozzles are essential in controlling how the abrasive media is projected onto the surface being treated. The nozzle dictates the speed, and spread of the abrasive blast, making it a key component in determining how well the surface is cleaned or prepared. In essence, the nozzle focuses the energy of the air and abrasive to achieve a uniform finish.
A nozzle's performance is measured by how well it delivers the abrasive material to the target surface while minimizing wastage and ensuring operator safety.
Types of Airblasting Nozzles
1. Venturi Nozzles:
Venturi nozzles are known for their ability to create a wide and uniform blast pattern. By expanding the airflow inside the nozzle, a Venturi nozzle increases the speed of the abrasive particles, resulting in faster cleaning and coverage over a larger area. This makes Venturi nozzles the preferred choice for high-production jobs, such as large-scale surface preparation in shipyards or industrial facilities.
Advantages:
- Covers large surface areas quickly.
- Increases productivity by speeding up the blasting process.
- Ideal for flat, open surfaces like ship hulls and large metal structures.
2. Straight Nozzles:
Straight nozzles produce a more concentrated and focused blast pattern. They are most effective for targeted cleaning or when working on specific areas where precision is essential. These nozzles are commonly used in situations where detailed blasting is required, such as in narrow spaces or when cleaning intricate parts of machinery.
Advantages:
- Provides more focused blasting for precise cleaning.
- Ideal for intricate or confined spaces.
- Allows the operator to concentrate on specific areas of a surface.
3. Long and Short Nozzles:
Long nozzles are typically used when the operator is working on open, wide surfaces that require greater reach. On the other hand, short nozzles are better suited for confined areas or workspaces where the operator needs more control over the blast direction. Both long and short nozzles are available in Venturi or straight designs, depending on the application.
Advantages:
- Long nozzles: Extend reach and cover larger areas.
- Short nozzles: Offer better maneuverability in tight spaces, such as tanks or chassis.
Materials of Nozzles: Tungsten Carbide vs. Boron Carbide
The material used to construct the nozzle impacts its durability and resistance to wear. Since the abrasive media traveling through the nozzle is highly destructive, choosing the right material for the nozzle can significantly extend its lifespan.
1. Tungsten Carbide Nozzles:
Tungsten carbide nozzles offer a good balance between cost and durability. They are resistant to wear and can handle most metallic abrasives, making them a popular choice for general-purpose blasting applications.
Benefits:
- High wear resistance.
- Suitable for use with metallic abrasives like steel shot or grit.
- Cost-effective for moderate-duty applications.
2. Boron Carbide Nozzles:
Boron carbide is one of the hardest materials available, providing superior resistance to wear compared to tungsten carbide. These nozzles are ideal for abrasive materials that are highly abrasive themselves, such as slag, aluminum oxide (corundum), or other non-metallic abrasives. While boron carbide nozzles are more expensive, their extended lifespan makes them cost-effective in the long run for demanding applications.
Benefits:
- Excellent resistance to wear.
- Suitable for aggressive abrasives like slag and corundum.
- Longer service life, particularly in heavy-duty applications.
Nozzle Maintenance and Replacement
Even the most durable nozzles wear out over time. As the nozzle's internal diameter expands due to wear, the air and abrasive flow become less efficient, resulting in reduced cleaning power and longer blasting times.
It’s recommended to replace a nozzle when its orifice diameter increases by more than 10% of its nominal size. Operating with a worn nozzle can lead to a loss of pressure, inefficiencies, and ultimately raising operational costs.
Signs That a Nozzle Needs Replacement:
- Reduced blasting power.
- Uneven or inconsistent blast pattern.
The Importance of Proper Nozzle Selection for Efficiency
Choosing the right nozzle is crucial not only for achieving the desired surface finish but also for ensuring maximum productivity and cost-efficiency. A properly selected nozzle will:
- Optimize Abrasive Flow: Ensuring that the correct amount of abrasive is delivered at the right pressure for efficient cleaning.
- Increase Productivity: By maintaining the proper blast pattern and pressure, the job can be completed more quickly, reducing labor time and increasing overall efficiency.
- Enhance Safety: With the correct nozzle, the operator maintains better control over the blast, reducing the risk of accidents or damage to the equipment.
Maximizing Performance and Minimizing Costs
Selecting the right nozzle type, material, and size can significantly impact performance, safety, and cost-efficiency. Partnering with experienced professionals who understand the nuances of nozzle selection can help you choose the most suitable nozzle for your application. Regular maintenance and timely replacement of nozzles will ensure that your airblasting system continues to operate at peak performance, saving you time and money in the long run.