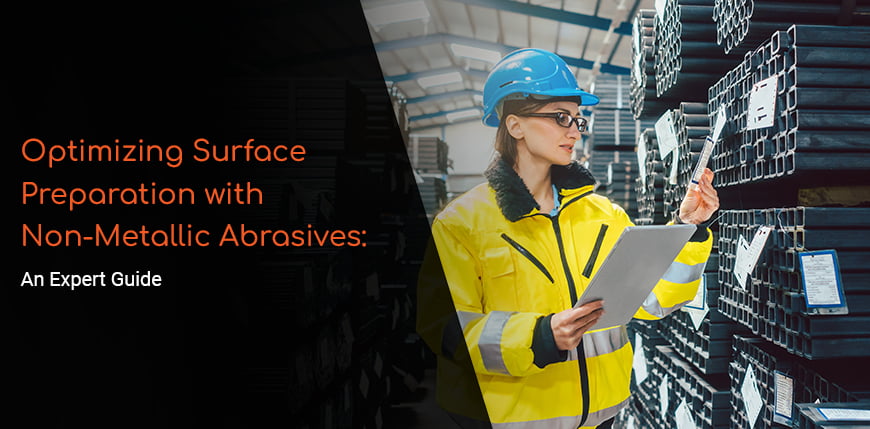
Non-metallic abrasives, including corundum, garnet, silica sand, and copper slag, offer unique advantages for a wide range of surface preparation needs. This article delves into the characteristics and applications of these abrasives, highlighting the importance of expert guidance in choosing the right product for specific industrial applications.
Understanding Non-Metallic Abrasives
Non-metallic abrasives are prized for their versatility and effectiveness in surface preparation tasks, ranging from aggressive material removal to precise surface conditioning. Their natural and synthetic compositions provide options for nearly every type of surface requirement.
- Corundum is known for its hardness and durability, making it ideal for preparing surfaces that require aggressive abrasion, such as removing stubborn coatings or preparing metal surfaces for high-performance coatings.
- Garnet offers a balance between abrasive action and surface finish quality. Its natural angularity and hardness make it suitable for a wide range of applications, from blasting to waterjet cutting, providing efficient material removal while maintaining a moderate surface profile.
- Silica Sand, once a staple in abrasive blasting, has seen reduced use in certain regions due to health concerns related to silica dust. However, its effectiveness in certain surface preparation contexts cannot be denied, particularly where specific surface textures are desired.
- Copper Slag is a byproduct of the metal smelting process, offering an eco-friendly alternative to traditional abrasives. Its angular shape and physical properties make it an excellent choice for removing rust, paint, and other coatings from metal surfaces.
The Role of Expert Guidance
The selection of the appropriate non-metallic abrasive is not a one-size-fits-all decision. Various factors, including the material of the substrate, the desired finish, environmental considerations, and cost, play into the decision-making process. Expert guidance is crucial in navigating these considerations, ensuring that the chosen abrasive aligns with the project's goals and regulatory requirements.
Specialists in abrasive blasting can provide invaluable insights into the most effective media for a given application, taking into account the specific characteristics of each abrasive and how they interact with different substrates. This tailored approach not only optimizes the surface preparation process but also enhances the efficiency and sustainability of the operation.
Choosing the Right Abrasive for Your Application
The selection process involves a thorough assessment of the project's requirements:
- For projects requiring a high degree of material removal without concern for dust generation, corundum or copper slag may be the preferred choices.
- In applications where the balance between abrasive action and surface integrity is paramount, garnet emerges as an optimal solution, particularly in industries like shipbuilding, where surface quality can significantly impact the longevity of the applied coatings.
- Silica sand, despite its drawbacks, may still find application in specific contexts where its properties are unmatched by other abrasives, though safety measures and regulatory compliance are paramount.
Conclusion
Non-metallic abrasives offer a range of solutions for surface preparation challenges, from aggressive material removal to precise surface conditioning. By leveraging the unique properties of corundum, garnet, silica sand, and copper slag, professionals can achieve optimal preparation results. However, the complexity of choosing the right abrasive underscores the importance of expert guidance. With the support of specialists, industries can navigate the selection process more effectively, ensuring that their surface preparation methods are both efficient and aligned with environmental and safety standards.