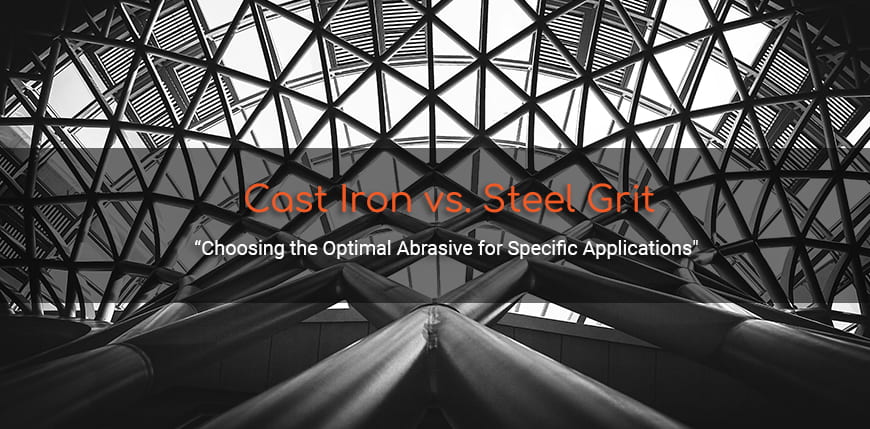
In the specialized field of abrasive blasting, selecting the appropriate abrasive media is critical to achieving desired surface preparation outcomes. The choice between cast iron and steel grit embodies a strategic decision, influenced by their performance characteristics, consumption rates, and the specific requirements of each application. This analysis delves into the distinctions between cast iron and steel grit, highlighting their respective advantages and guiding professionals in making informed decisions.
Performance and Consumption Rates
Cast Iron Abrasives are noted for their aggressive profiling capabilities, producing a sharper surface finish that is often required for applications such as bonding. This pronounced profile can enhance the mechanical adhesion of coatings, making cast iron an ideal choice for operations where surface preparation is critical to the bonding process. However, cast iron tends to have a higher consumption rate compared to steel grit, attributed to its brittleness and faster breakdown during the blasting process.
Steel Grit, on the other hand, offers durability and a somewhat less aggressive profile, leading to lower consumption rates over time. This makes steel grit a cost-effective option for general surface preparation, renovation, and where a less pronounced surface profile is sufficient. The choice between the two often comes down to balancing the need for a sharp profile against the efficiency and cost implications of the abrasive's consumption rate.
Applications and Machine Compatibility
Both cast iron and steel abrasives are commonly used in airblasting applications, with their selection tailored to the specific needs of surface prep, renovation, and bonding. For projects requiring aggressive surface treatment to achieve a high degree of adhesion, such as in bonding applications, cast iron may offer the preferred solution due to its sharper profile.
A notable mention is the specific use of shot variants of these abrasives in waste treatment incinerators, where both cast iron shot and steel shot are employed for gravity-assisted descaling. This application underscores the versatility of these materials in meeting the unique challenges of different industrial processes.
Optimizing the Blasting Process
Given the nuanced differences between cast iron and steel grit, professional guidance is invaluable in optimizing the blasting process. Expert consultation can assist in selecting the most suitable abrasive media, adjusting blasting parameters to maximize efficiency, and ensuring that the chosen media meets the specific requirements of the application. This tailored approach ensures that the blasting operation achieves the desired outcomes, whether for general surface preparation or specialized applications requiring specific surface profiles.
Conclusion
The decision to use cast iron or steel grit in abrasive blasting hinges on a thorough understanding of each material's performance characteristics, consumption rates, and the specific requirements of the intended application. By carefully considering these factors, professionals can choose the abrasive that best aligns with their operational goals, ensuring optimal results in surface preparation and beyond. Leveraging expert advice further enhances the process, enabling the fine-tuning of blasting operations to achieve efficiency, cost-effectiveness, and superior surface quality.