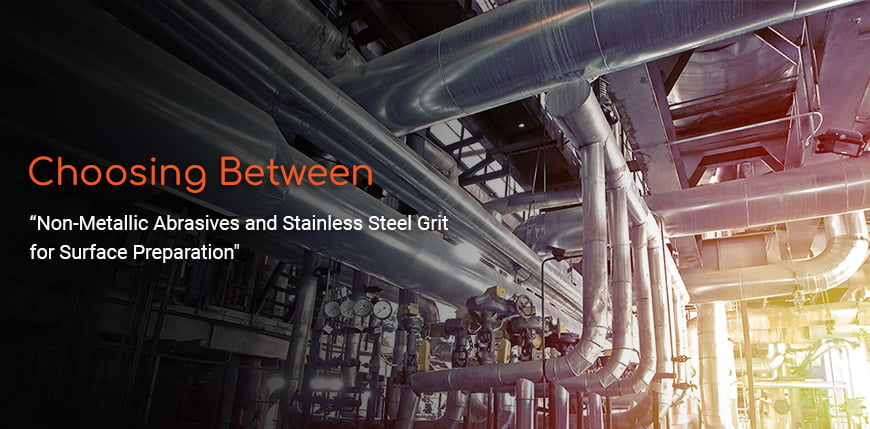
In the realm of surface preparation, the choice of abrasive material is pivotal, directly impacting the efficiency, environmental footprint, and outcome of the blasting process. Non-metallic abrasives and stainless steel grit each offer distinct advantages and limitations, making them suitable for different scenarios based on surface sensitivity, ecological considerations, and the specific requirements of various industries.
Environmental Impact and Abrasiveness: A Comparative Overview
Non-Metallic Abrasives: Renowned for their versatility, non-metallic abrasives are particularly advantageous for outdoor blasting operations where the investment in blasting cabins is not feasible. They are well-suited for tasks such as sandblasting, where the risk of oxidation is a concern, and offer a slightly lower cost point. Non-metallic abrasives are also compatible with water jet cutting applications, presenting an ecological benefit through the potential for greater waste recycling. However, their use might be limited by their slightly less aggressive abrasiveness compared to metallic alternatives.
Stainless Steel Grit: Stainless steel grit, on the other hand, requires a blasting cabin and a dedicated recycling system, representing a higher initial investment. Despite this, the grit's durability leads to significantly lower consumption rates—between 10 to 50 times less—compared to non-metallic abrasives. The low friability of stainless steel grit means it produces minimal dust, reducing health risks and improving work conditions by maintaining clearer air within the blasting environment.
Applications and Industry Suitability
The choice between non-metallic abrasives and stainless steel grit largely depends on the application and industry. Non-metallic abrasives, with their adaptability and ecological advantages, are particularly suited for industries like construction, where outdoor blasting is common, and the prevention of oxidation is crucial. Their environmental friendliness and ease of waste management make them a preferred choice for projects with significant ecological considerations.
In contrast, stainless steel grit is favored in industries requiring high precision and minimal environmental contamination, such as automotive, aerospace, and rail. The reduced dust generation and lower consumption make stainless steel grit an economically and environmentally sound option for these sectors, particularly when the blasting process is contained within a cabin.
Optimizing the Blasting Process with Expert Guidance
Regardless of the choice between non-metallic abrasives and stainless steel grit, optimizing the blasting process to achieve the best possible outcomes necessitates expert guidance. Professional consultation can help navigate the complexities of selecting the appropriate abrasive material, considering factors like the specific surface to be treated, the desired finish, and environmental regulations. This expertise ensures that the blasting operation is not only effective but also aligned with best practices for sustainability and worker safety.
Conclusion
The decision to use non-metallic abrasives or stainless steel grit for surface preparation should be informed by a thorough understanding of each material's properties, environmental implications, and the specific requirements of the application at hand. By considering these factors and seeking professional advice, industries can enhance their surface preparation processes, achieving optimal results while adhering to ecological and safety standards.