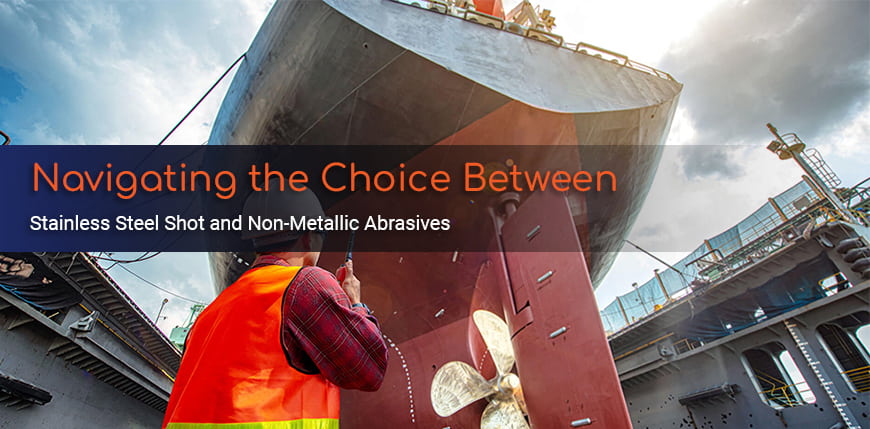
In the diverse world of abrasive blasting, the selection of the abrasive media plays a pivotal role in determining the outcome of surface treatment processes. When it comes to treating sensitive surfaces, the choice between stainless steel shot and non-metallic abrasives becomes crucial. This comparative analysis evaluates their performance, cost implications, and environmental impacts, guiding professionals towards making informed decisions tailored to their specific needs.
Performance on Sensitive Surfaces
Stainless Steel Shot is known for its uniformity and high density, which allows for precise control over the blasting process. Its limited potential for causing corrosion makes it a suitable option for treating sensitive surfaces, especially where maintaining the integrity of the substrate is paramount. However, the higher cost of stainless steel shot, attributed to its composition and the need for specialized handling, necessitates careful process management to optimize consumption and minimize expenses.
Non-Metallic Abrasives, on the other hand, offer a broader range of hardness levels, making them adaptable to a variety of surface sensitivities. While they are effective in reducing the risk of surface contamination and are generally less costly upfront, their use can result in significant dust generation and higher equipment wear. This increased maintenance requirement, coupled with the need for more frequent waste recycling, can offset the initial cost benefits.
Cost of Use and Environmental Considerations
The cost of using Stainless Steel Shot extends beyond the initial purchase, encompassing the lifecycle of the abrasive and its impact on the blasting equipment. Its durability and reusability can lead to long-term savings for operations that can justify the initial investment through reduced abrasive consumption over time.
Non-Metallic Abrasives may appear more cost-effective initially but can lead to increased operational costs due to higher consumption rates, more significant dust production, and the associated health and safety measures required. The environmental impact of waste generated by non-metallic abrasives also necessitates consideration, particularly for industries prioritizing sustainable practices.
Situations Dictating the Choice
The decision to use stainless steel shot or non-metallic abrasives hinges on several factors:
- For surfaces that cannot tolerate any risk of corrosion or where a high-quality finish is critical, stainless steel shot may be the preferred choice, despite its higher cost. Industries like aerospace, automotive, and mold cleaning, which demand precise surface treatment, often lean towards stainless steel for its consistent performance and minimal impact on the substrate.
- Non-metallic abrasives might be favored in situations where the delicacy of the surface does not align with the characteristics of metallic shots or where environmental and health considerations dictate the use of less aggressive media. Their versatility makes them suitable for a wide range of applications, from construction to the cleaning of non-ferrous materials.
Expert Guidance for Process Optimization
Regardless of the choice between stainless steel shot and non-metallic abrasives, leveraging expert guidance is key to optimizing the blasting process. Professional consultation can help in selecting the right abrasive, adjusting blasting parameters, and implementing best practices to maximize efficiency, cost-effectiveness, and environmental compliance.
Conclusion
In abrasive blasting, the choice between stainless steel shot and non-metallic abrasives requires careful consideration of performance requirements, cost implications, and environmental impacts. By evaluating the specific needs of each application and seeking expert advice, professionals can select the most appropriate abrasive media, ensuring optimal results for sensitive surface treatments.