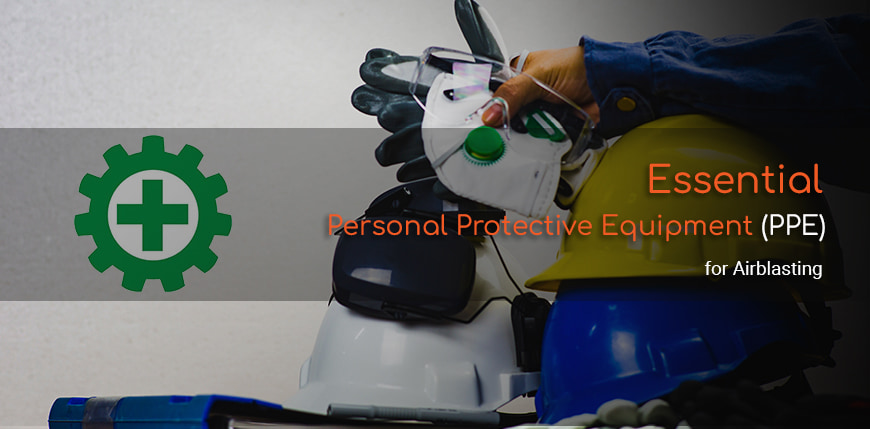
The Importance of PPE in Airblasting
Airblasting operations involve the use of compressed air to propel abrasive media at high speeds, which can pose significant health and safety risks. Without proper PPE, operators are exposed to potential dangers such as flying debris, loud noise, and abrasive particles, which can lead to serious injuries or long-term health issues. Using appropriate PPE not only protects workers but also ensures compliance with safety regulations and enhances overall operational efficiency.
Essential PPE Components for Airblasting
1. Safety Boots with Protective Pants
- Description: Safety boots are essential for protecting the feet from falling debris sharp particles and before all the fall of heavy parts on operator’s feet. Even if the abrasive particles are light, the parts manipulated inside the blasting cabinet are very heavy and sometimes in a precarious balance. The pants should cover the boots and be again better secured with adhesive tape to prevent abrasive media from penetrating the boots. This additional layer of protection ensures that no abrasive particles can enter the footwear, reducing the risk of foot injuries.
- Importance: Safety boots prevent severe injuries due to the fall of heavy parts. The adhesive tape Prevents abrasive media from penetrating the boots, ensuring that operators' feet remain protected from potential injuries and contamination.
2. Long-Sleeve Work Suit with Splash-Proof Apron
- Description: A long-sleeve work suit provides full-body protection from abrasive media and debris. The addition of a splash-proof apron protects the operator’s torso and legs from abrasive impacts and reduces the risk of exposure to harmful materials.
- Importance: Protects against abrasions and impacts, ensuring that workers are shielded from potentially harmful substances and projectiles.
3. Cut-Resistant Gloves with Adhesive Tape
- Description: Gloves designed to resist cuts and abrasions are crucial for protecting the hands during airblasting operations. Often, additional adhesive tape is used to enhance the gloves' resistance to abrasions and prevent contaminants from entering.
- Importance: Safeguards the hands from sharp abrasive particles and other hazards, reducing the risk of cuts and injuries during operation.
4. Safety Helmet with Face Shield and Neck Protector
- Description: The safety helmet, resembling a full-face respirator, provides head protection and features a replaceable face shield. A neck protector, or “napron,” ensures full coverage and prevents abrasive media from entering around the neck area.
- Importance: Protects the head and face from flying debris and impacts, and the neck protector ensures complete coverage to avoid exposure to harmful materials.
5. Purified Air System with Cooling
- Description: A purified air system provides clean, breathable air to the operator inside the safety halmet, which is crucial in dusty environments. The system typically includes a cooling mechanism to enhance comfort during extended operations.
- Importance: Ensures that operators breathe clean air, reducing the risk of respiratory issues and improving overall comfort in a high-dust environment.
6. Hearing Protection (Foam Ear Plugs)
- Description: Foam ear plugs or other types of hearing protection are essential in airblasting environments where noise levels can be high. These protectors help prevent
- Importance: Protects against hearing loss caused by prolonged exposure to high noise levels, maintaining the operator’s long-term auditory health.
7. Reflective Bands
- Description: Reflective bands are recommended on the working clothes for use in dark environments, enhancing visibility and ensuring that operators are easily seen by others.
- Importance: Increases visibility in low-light conditions, reducing the risk of accidents and improving overall safety in the workplace.
Best Practices for PPE Usage
1. Regular Inspections: Conduct regular checks of all PPE to ensure that it is in good condition. Replace any damaged or worn-out equipment promptly to maintain effective protection.
2. Proper Fit and Adjustment: Ensure that all PPE fits correctly and is properly adjusted. Ill-fitting equipment can compromise safety and comfort, leading to increased risk during operations.
3. Training and Awareness: Provide training for operators on the correct use and maintenance of PPE. Ensuring that all personnel understand the importance of their protective gear helps maintain safety standards and reduces the likelihood of accidents.
4. Compliance with Regulations: Adhere to industry regulations and standards for PPE. This ensures that all protective equipment meets the required safety criteria and provides adequate protection.
Conclusion and Expert Guidance
By investing in high-quality PPE, conducting regular inspections, and adhering to safety regulations, you can safeguard your workforce and maintain a safe and productive working environment. For further assistance in selecting the right PPE and implementing effective safety measures, consulting with industry experts can provide valuable insights and support. Expert guidance helps ensure that your PPE meets the highest safety standards and is tailored to your specific operational needs.