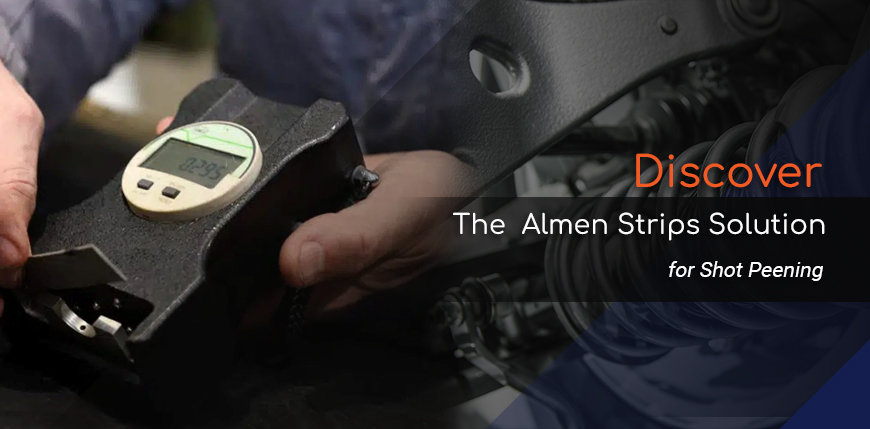
Understanding Almen Strips in Shot Peening: Purpose, Types, and Technical Differences
Almen strips are small but essential tools help measure the energy imparted during the shot peening process, ensuring that the process meets the required specifications. In this article, we’ll dive into the purpose of Almen strips, explore the technical differences between them, and discuss how they are used to achieve precise shot peening outcomes.
The Purpose of Almen Strips in Shot Peening
What Are Almen Strips?
Almen strips are specialized devices used to measure the intensity of the shot peening process. They work by deforming in response to the energy imparted by the shot, which is then measured to determine whether the process is within the specified parameters. The amount of deformation—referred to as the "arc height"—is measured using a specific tool known as an Almen gage. This arc height must meet the precise specifications set by the customer or engineering standards to ensure the shot peening process is effective.
How They Work:
When a component undergoes shot peening, the Almen strip is placed in the same blast stream as the part being treated. The energy from the peening process causes the strip to bend. The degree of this bend is directly proportional to the energy delivered by the shot. By measuring the arc height of the strip after peening, technicians can determine whether the process is delivering the correct amount of energy to the component.
Versatility in Usage:
Shot peening can be conducted using various types of media, including AMS shot, steel shot, and conditioned cut wire. Regardless of the media used, the Almen strip provides a reliable measurement of the energy imparted during the process, ensuring consistency and adherence to specifications.
Example:
For instance, if the required specification is F10N (N is for metric countries), this means the strip should exhibit an arc height of 0.1 mm after peening, using an N-type Almen strip, if the required specification is 10N (no F before means imperial units) this means the strip should exhibit an arc height of 0.01 inch after peening, using an N-type Almen strip . This specification ensures that the process is delivering the exact amount of energy needed for the application.
Technical Differences Between Almen Strips
Types of Almen Strips:
There are three primary types of Almen strips, each designed for different levels of energy absorption and specific use cases:
1. N-Type Almen Strips:
- Description: The thinnest and most easily deformed type, N-type strips are used with very fine shot media. They are typically recommended for use with shot sizes below 0.5 mm in diameter.
- Use Case: These are typically employed when the shot size is small and the peening intensity is lower, making them ideal for delicate or finely detailed components.
2. A-Type Almen Strips:
- Description: The most commonly used strip, A-type strips cover about 80% of shot peening applications. They are recommended for use with shot sizes ranging from 0.5 mm to 1.4 mm in diameter.
- Use Case: They are versatile and suitable for a wide range of shot sizes and intensities, making them the go-to choice for most general applications. If after blasting operation an arc height lower than 0.1mm is reached with Almen strip A, so switch to N type to get a better sensibility of the strip. If an arc height above 0.6mm is reached with Almen strip A, so switch to C type to get a lower deformation and make it easily measurable by the Almen gauge.
3. C-Type Almen Strips:
- Description: The thickest and most resistant to deformation, C-type strips are designed for use with larger shot sizes, typically greater than 1.4 mm in diameter.
- Use Case: These strips are used in high-intensity shot peening applications where significant energy is required, often for large, heavy-duty components.
Selecting the Right Almen Strip:
The choice of which Almen strip to use is typically determined by engineering specifications, often set by the design or production team. The type of strip is chosen based on the shot size and the desired peening intensity. While there is no direct correlation between the arc height measured on the Almen strip and the eventual lifespan of the part, the correct selection and use of Almen strips ensure that the peening process meets the necessary quality standards.
Certification and Standards for Almen Strips
Certification Levels:
To ensure accuracy and reliability, Almen strips are manufactured to strict standards, and there are specific certifications available:
1. Standard Strips:
- Basic Almen strips that meet the standard requirements for most general applications.
2. Certified 2 Strips:
- These strips are certified for more stringent applications, ensuring tighter control over the material composition, size, hardness and flatness.
3. Certified 1 Strips:
- The highest level of certification, these strips are used in highly critical applications where maximum precision is required.
Each certification level ensures that the Almen strips conform to specific size, flatness, chemical compositions and hardness requirements, allowing for consistent and repeatable measurements.
Conclusion and Expert Guidance
Whether you’re working with delicate components that require fine shot or large, heavy-duty parts that need high-intensity peening, selecting the right Almen strip is key. For companies looking to optimize their shot peening processes, consulting with experts who can provide guidance on the correct use of Almen strips and the calibration of Almen gauges is crucial. By partnering with knowledgeable professionals, you can ensure that your shot peening processes meet the highest standards of quality and precision.