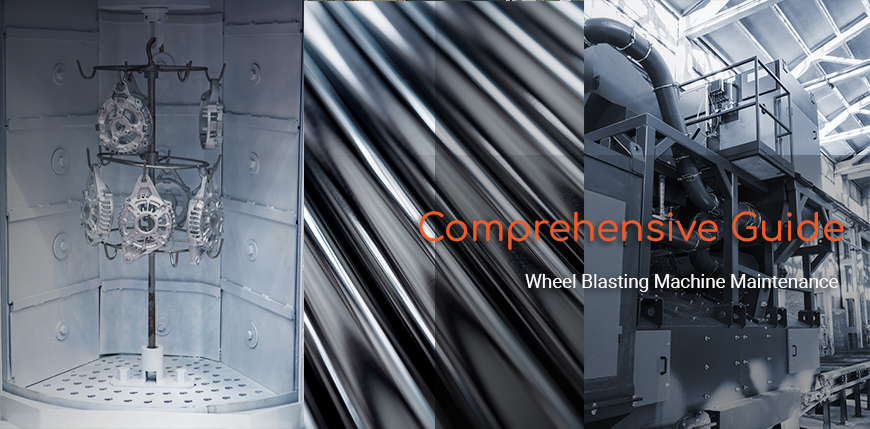
Wheel blasting machines, often the backbone of surface preparation processes in various industries, require meticulous care and attention to detail to function optimally. Whether you’re dealing with regular wear and tear or managing unexpected breakdowns, understanding the nuances of wheel blasting machine maintenance can significantly impact your operations' productivity and cost-effectiveness.
This article introduces you to a comprehensive guide designed to provide insights into the critical aspects of wheel blasting machine maintenance. From understanding the difference between wear and spare parts to adopting proactive maintenance strategies, this guide covers everything you need to know to keep your machines running smoothly.
Understanding Wear and Spare Parts
One of the fundamental aspects of maintaining wheel blasting machines is knowing the difference between wear parts and spare parts. Wear parts are those components that, due to their constant exposure to abrasive materials and high-speed operations, are expected to wear out over time. These include blades, control cages, and impellers. Replacing these parts at the right time is crucial to maintaining the quality of the blasting process and preventing costly damage to other machine components.
On the other hand, spare parts are components that have a longer lifespan and are not subjected to the same level of wear and tear as wear parts. Examples include screws, elevators, sliding plates, and blindage plates. While these parts don’t require frequent replacement, monitoring their condition is essential to avoid unexpected breakdowns.
For a more detailed exploration of the differences and how to manage these parts effectively, read our first article: Understanding the Difference Between Wear Parts and Spare Parts in Wheel Blasting Machines.
Proactive vs. Reactive Maintenance: Why It Matters
In the world of industrial machinery, the old adage “prevention is better than cure” holds especially true. Proactive maintenance involves regular checks and the timely replacement of parts before they fail. This approach not only prevents unexpected downtime but also ensures that the machine
operates at peak efficiency. On the contrary, reactive maintenance, which involves fixing problems as they occur, can lead to costly production stops, increased wear on other components, and even safety risks.
Implementing proactive maintenance strategies, such as weekly inspections of wear parts and using tools like thermal cameras to determine the position of the hot spot or check regularly the size distribution of the operating mix of abrasive, can save you significant time and money in the long run.
For an in-depth look at these strategies, check out our article: Effective Maintenance Strategies for Wheel Blasting Machines: Proactive vs. Reactive Maintenance.
Optimizing Performance Through Proper Wear Parts Management
The performance of a wheel blasting machine heavily depends on the condition of its wear parts. Over time, components like blades, control cages, and impellers will wear down, affecting the quality of the blasting process. Proper management of these parts, including regular inspections and timely replacements, is key to ensuring consistent performance and avoiding costly repairs.
Managing wear parts also involves understanding the economic implications of using high-quality versus low-quality components. While cheaper parts may seem like a good deal initially, they often wear out faster and lead to more frequent replacements and potential damage to other machine parts.
To learn more about optimizing your machine’s performance through effective wear parts management, read our article: Optimizing Wheel Blasting Performance Through Proper Wear Parts Management.
The Role of Spare Parts in Machine Longevity
While wear parts are critical for daily operations, spare parts play a significant role in the long-term maintenance and longevity of your wheel blasting machines. Managing these parts effectively, including maintaining an inventory of critical components and understanding when to replace them, can prevent unexpected downtime and extend the life of your equipment.
Innovations in spare parts, such as the use of advanced materials like tungsten carbide, have further enhanced the durability and performance of these components. However, these advanced parts require a well-maintained machine to deliver their full benefits, making regular machine check-ups and adjustments essential.
For more insights on how to manage your spare parts effectively, refer to our article: The Essential Guide to Managing Spare Parts for Wheel Blasting Machines
Conclusion and Expert Guidance
Maintaining wheel blasting machines is not just about replacing parts when they wear out; it’s about adopting a comprehensive and proactive approach to ensure the longevity, efficiency, and safety of your equipment. By understanding the differences between wear and spare parts, implementing
proactive maintenance strategies, and optimizing your machine’s performance, you can significantly reduce downtime and extend the life of your equipment.
For those looking to deepen their knowledge and fine-tune their maintenance practices, consulting with industry experts can provide invaluable insights. Whether you’re dealing with complex issues or seeking to optimize your processes, expert guidance can help you achieve the best possible results.