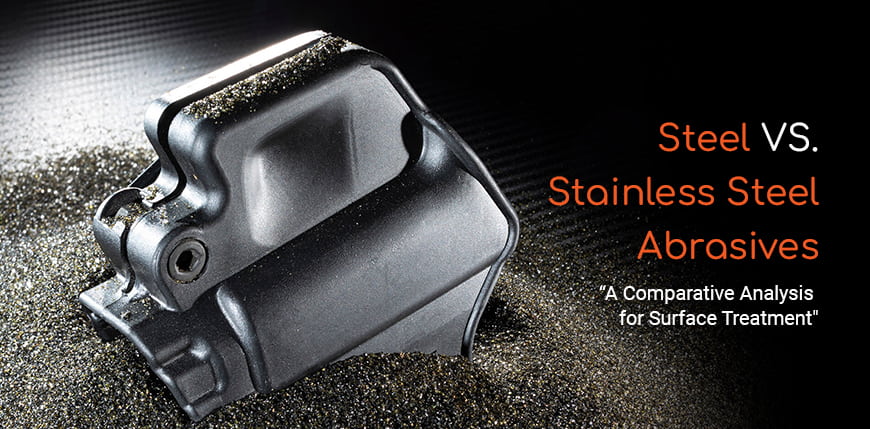
In the intricate world of abrasive blasting, the choice between steel shot/grit and stainless steel shot/grit can significantly influence the outcome of surface treatment processes. These abrasives, while similar in name, possess distinct characteristics that cater to diverse industrial needs. Understanding their differences in cost, corrosion resistance, and specific uses is essential for selecting the most suitable abrasive for a given application.
Cost and Corrosion Resistance: Key Factors
Steel Shot/Grit: Traditional steel shot and grit are widely recognized for their cost-effectiveness and efficiency in various blasting applications. Their robust nature makes them ideal for aggressive surface cleaning, descaling, and preparation. However, the primary limitation of steel shot/grit lies in its susceptibility to corrosion, especially when used on surfaces that require high levels of corrosion resistance.
Stainless Steel Shot/Grit: Stainless steel abrasives, incorporating elements like nickel and chromium, offer enhanced corrosion resistance, making them particularly suited for treating non-ferrous materials and surfaces where minimizing corrosion is paramount. The inclusion of these elements does lead to a slightly higher cost compared to traditional steel abrasives. Nonetheless, the investment in stainless steel shot/grit can be justified by the superior corrosion resistance and the specific requirements of the application.
Consumption and Efficiency
Both steel and stainless steel abrasives demonstrate similar levels of consumption and efficiency when used in appropriate settings. The choice between them often hinges on the balance between initial cost considerations and the long-term benefits of reduced corrosion.
Industries and Applications: Tailoring the Choice
Stainless Steel Shot/Grit is particularly advantageous in industries where the prevention of corrosion on the treated surfaces is critical. Applications in the automotive, aerospace, and rail industries, as well as construction and mold cleaning, benefit from the use of stainless steel abrasives. These sectors often deal with non-ferrous materials or require a pristine finish that only stainless steel can provide without the risk of inducing surface corrosion.
Steel Shot/Grit, with its cost-effectiveness and aggressive cleaning capabilities, remains a staple in applications where surface preparation and the removal of heavy scale or rust are the primary goals. Its use is widespread across various industries, including the cleaning of ferrous materials, where the additional cost of stainless steel does not translate into significant benefits.
Machine Compatibility
Both wheelblasting and airblasting machines are compatible with steel and stainless steel abrasives, allowing for versatility in application techniques. The choice of machine, whether wheelblasting for high-volume treatments or airblasting for precision work, depends on the specific requirements of the surface treatment process.
Navigating the Selection with Expert Guidance
Given the nuanced differences between steel and stainless steel shot/grit, professional guidance is crucial for optimizing the blasting process. Expert advice can help identify the most suitable abrasive type, considering the material to be treated, the desired finish, and the overall objectives of the blasting operation. This tailored approach ensures that industries can leverage the unique advantages of each abrasive type, maximizing the efficiency and effectiveness of their surface treatment processes.